Bearing damage and failure analysis (bearing damages) or abnormal brinelling bearing damage for cylindrical roller bearings is an elaborate technical process, especially for handling accident scenes. Like the Timken one, many bearing manufacturers offer a printable version of the maintenance manual. Based on our company's years of on-site processing experience, we have summarized a few critical points for your reference regarding cylindrical roller failure.
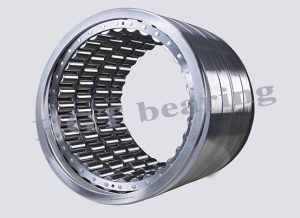
Disassembly of damaged cylindrical roller bearings
To understand the bearing damages better, special attention is needed during the disassembly. The specific attention is not only to its correct position and disassembly order of bearing components (especially for multi-row rolling mill neck bearings); it is also essential to check if there is still residual lubricant on the bearing components (dry or coking).
The relationship between the load area and the damaged parts should be analyzed to collect complete failure information. Few essential things we summarize here.
1. Investigation of the relevant parts
The main contents of the investigation on the parts include the dimensions and form/position error of the cylindrical roller bearing. And also the installation and arrangement of the bearing housing, the integrity of the sealing device, etc.
2. Investigation of the lubrication area
The investigation contents include whether the oil level of the fuel tank (cavity) is reasonable. Whether the lubrication pipe and the distribution system are unblocked. The brand and grade of lubricant, the lubrication parameters (replacement period, dosage, etc.), and the test record should be checked.
3. Collection of operating parameters
The operating parameters mainly include loading capacity, rotational speed, bearing vibration, etc. The equipment inspection records with working temperature and the actual running time should be checked.
Based on the observation, it is essential to make inspection records and determine the cause of failure in detail. Please contact us at [email protected] regarding bearing damage and failure analysis or brinelling bearing damage.